3D printing at Signify’s Turnhout factory is changing the face of manufacturing
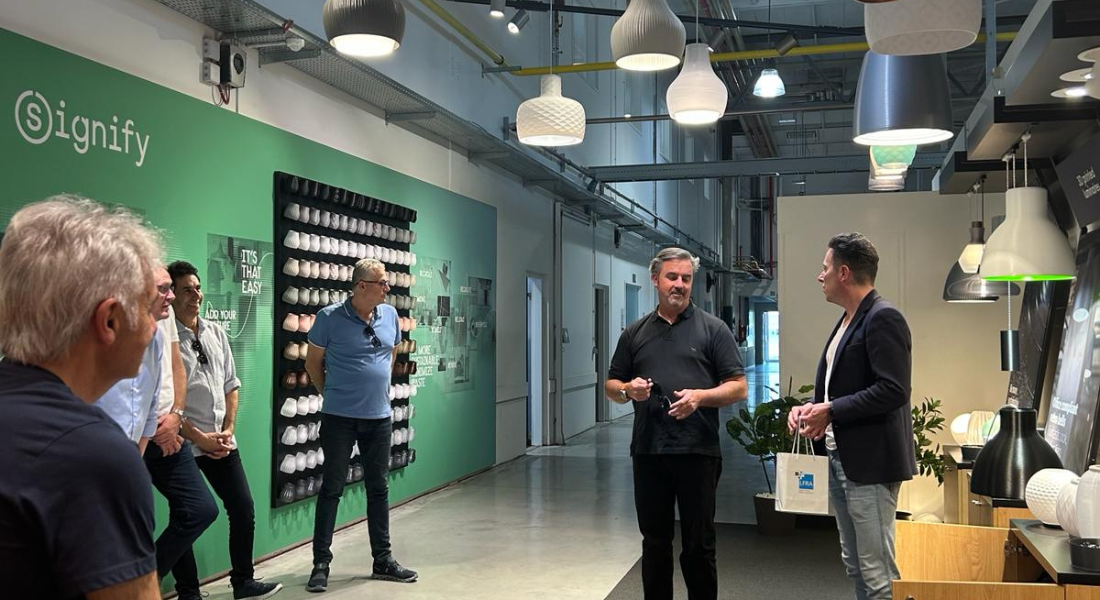
One of the highlights of last year’s LFRA European Study Tour was a tour of Signify’s 3D printing factory in Turnhout in Belgium.
The adoption of 3D printing by Signify (formally known as Philips Lighting) as the new norm for its exacting manufacturing standards six years was a landmark event in the history of a company with a commitment to constant innovation.
Signify, knew that the process would require thorough investigation and testing by their Engineering Designer, Danny Van der Jonckheyd.
A company founded in 1891, Signify re-imagined its approach to traditional methods of design and manufacturing lighting fixtures, opening up possibilities for customization.
3D printing excels in replicating intricate that are not feasible with conventional techniques while allowing for efficiencies through less wastage.
This aligned with Signify’s commitment to sustainability through eco-friendly design and manufacturing practices.
Study Tour participants were told that the design process is crucial in achieving optimal lighting solutions.
3D printing accelerates by rapid prototyping, which allows its manufacturing engineers to concentrate on eliminating process bugs rather the minute detailing of misprints.
Designers can also quickly create physical prototypes of their designs, allowing for hands-on evaluation and modification.
This iterative approach results in faster development cycles and ensures that the final lighting fixtures meet expectations.
The ability to prototype efficiently encourages collaboration between designers, engineers, and clients, fostering a more interactive and responsive design workflow.
3D printing widens the range of materials suitable for lighting fit-outs. From translucent and transparent resins to durable and lightweight polymers, the material choices are vast and diverse.
This variety opens the door to innovative solutions such as light-diffusing structures, unique textures, and materials with specific optical properties.
Designers can experiment with materials to achieve their desired visual effects, ensuring that the lighting fixtures not only illuminate but also contribute to the overall ambiance of the space.
While the initial investment in 3D printing technology was significant, the long-term efficiencies are substantial.
3D printing allows for on-demand production – before costly re-tooling. This reduces inventory costs and cuts waste.
Notably, Signify has supplied prominent fast food chain, McDonald’s, with all its lighting fixtures in its restaurants. This resulted in fitting over 38,000 restaurants across the globe, a global scale only deliverable from the Signify factory.
Further to this, McDonald’s have an ambitiuous target to reduce their carbon footprint by 60% before 2030, meaning that the implementation of 3D printed light fittings would contribute to the reduction in this number.
The integration of 3D printing into lighting fit-outs marks a significant leap forward in design possibilities. Signify is committed to growing its 3D printing facilities as the technology evolves.